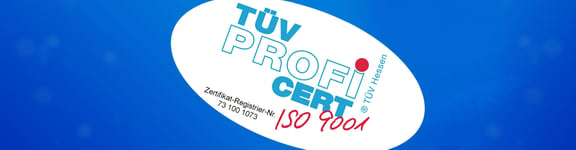
Quality management at tci:
Transparency, efficiency and innovation through centralised project management
tci GmbH attaches great importance to effective quality management in order to continuously improve the quality of its products as well as its production and support processes. Since 2016, all relevant processes and documentation have been organised centrally in the ERP software. This includes, among other things:
- 8D reports for problem solving,
- Product change notifications (PCN),
- Processing of CIO enquiries and DOA cases,
- Management of process-related measures,
- Carrying out process self-checks and tool checks
- Processing and managing the audit programme and management review
- Recording and tracking defective hardware.
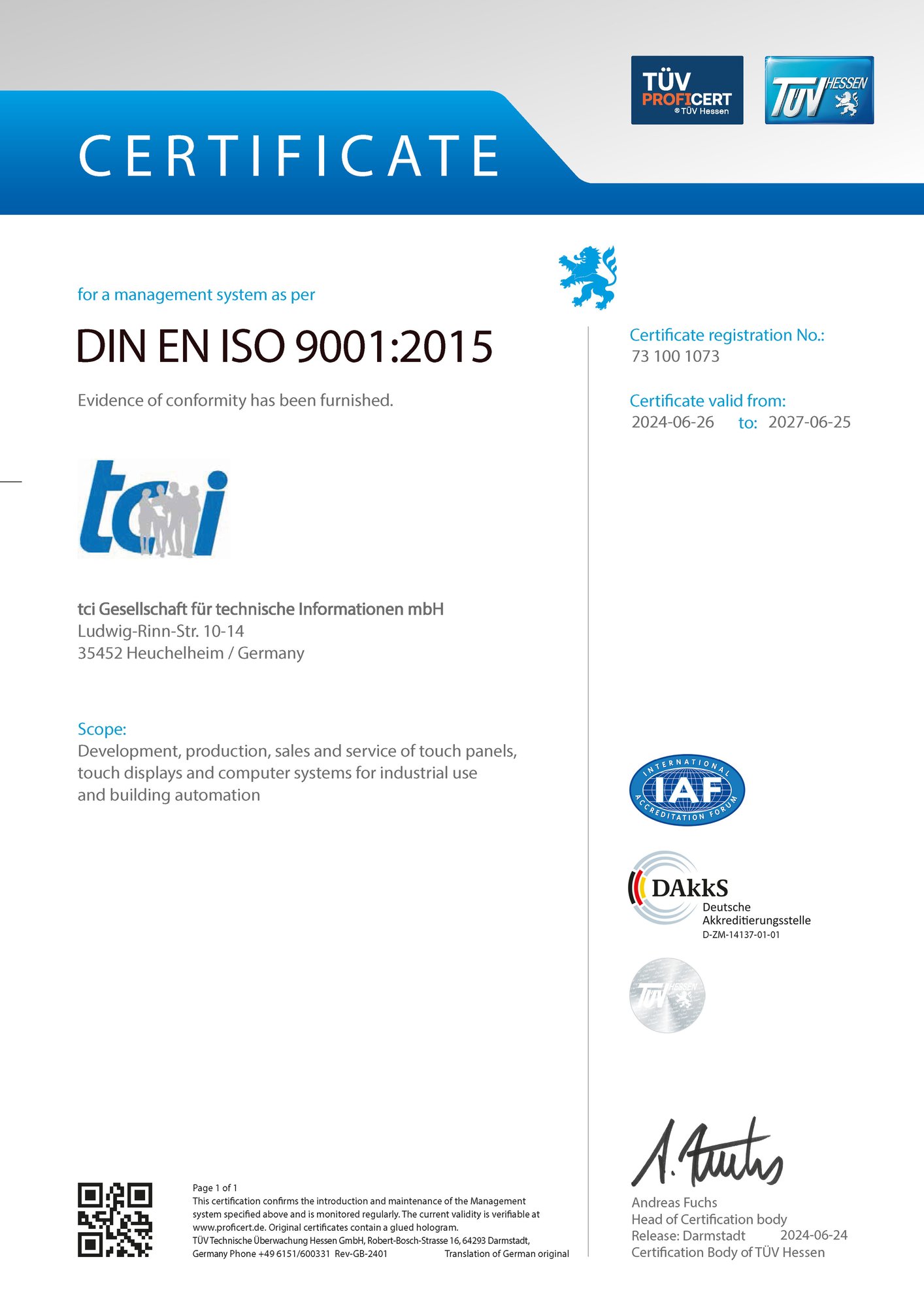
Structured project management
All of these tasks are mapped as projects in the ERP, with different project types developed with specific checklists and tabs. These projects offer customised notifications with three escalation levels and automated monitoring so that tasks and data are distributed to the responsible parties in near real time.
Advantages of centralised management
The consistent mapping of all processes in the ERP enables
- Maximum transparency and traceability,
- Efficient training and documentation,
- A structured workflow for all employees, as handling is schematic and standardised.
Support beyond the core process
Supporting departments such as HR, marketing and occupational health and safety have also been integrated into the system. This creates a holistic approach that optimises both management and support processes.
The result is a circular improvement process that ensures transparency, efficiency and clear responsibilities - a significant contribution to the high quality and reliability of tci products and services.